Maximizing performance, reliability and durability are paramount in the highly demanding mining and mineral processing industry. Any outage of critical equipment, such as pumps, can bring an entire plant to a halt, resulting in disastrously high costs for plant operators. This is why they are on the lookout for supplier-partners able to offer them heavy-duty solutions maximizing productivity and profitability.
With its pump solutions for applications in mine water management, such as mine and process dewatering, process water, and water reclamation, Trillium Flow Technologies aims to support customers to do just that and contribute to enhancing total plant efficiency, reliability, and sustainability.
A new mine process
A Trillium customer developed a new copper leaching process to increase yield from ore using an acidic solution with a pH of approximately 1.2 and a high level of chlorides. This combination of low pH and high levels of chlorides required the use of titanium for pump construction. The customer contacted the engineering team for Trillium’s Floway brand, which specializes in vertical turbine pumps with maximum durable wear and corrosion resistance, to lead the pump development project. Trillium conducted significant research and development studies regarding material characteristics to find the balance between cost and suitability of different titanium grades, sourced and qualified new suppliers, and tested and inspected first article castings prior to production.
Coordination with the client was crucial to ensure the proper design and material grade selection for various pump components and the creation of discharge heads to fit their existing motors. The pumps themselves – Floway 5 Stage 18MKL and 6 Stage 18MKL – were rigorously tested in accordance with industry standards using calibrated lab drivers.
API-610 standards
Trillium’s Gabbioneta Pumps brand specializes in fully API 610-compliant pump packages for the oil and gas market and also serves the mining sector due to the parallels between the oil and gas and mining industries’ highly demanding requirements.
Trillium recently supplied heavy-duty process multistage horizontal, between bearings pumps for a new copper and molybdenum mine project in Latin America, where the customer specifically requested pumps with API 610 standards due to the extreme operating conditions.
The supply consists of BB3-type Gabbioneta Pumps AHP-DS model pump packages installed at the facilities’ pumping stations to provide water pumping service. The 7-stage pumps are equipped with non-metallic bushings to optimize efficiency, and the pump packages each include a motor equipped with a VFD which constantly regulate speed, an API 682 mechanical seal with plan 11, a lube oil system for the pump thrust bearings forced lubrication, and radial and thrust bearings vibration and temperature sensors for monitoring purposes.
R&D studies were conducted to develop the pump package, including computational fluid dynamics (CFD) and finite element method (FEM). In addition, pump performance tests and complete unit tests were performed in-house at Trillium’s Nova Milanese facilities.
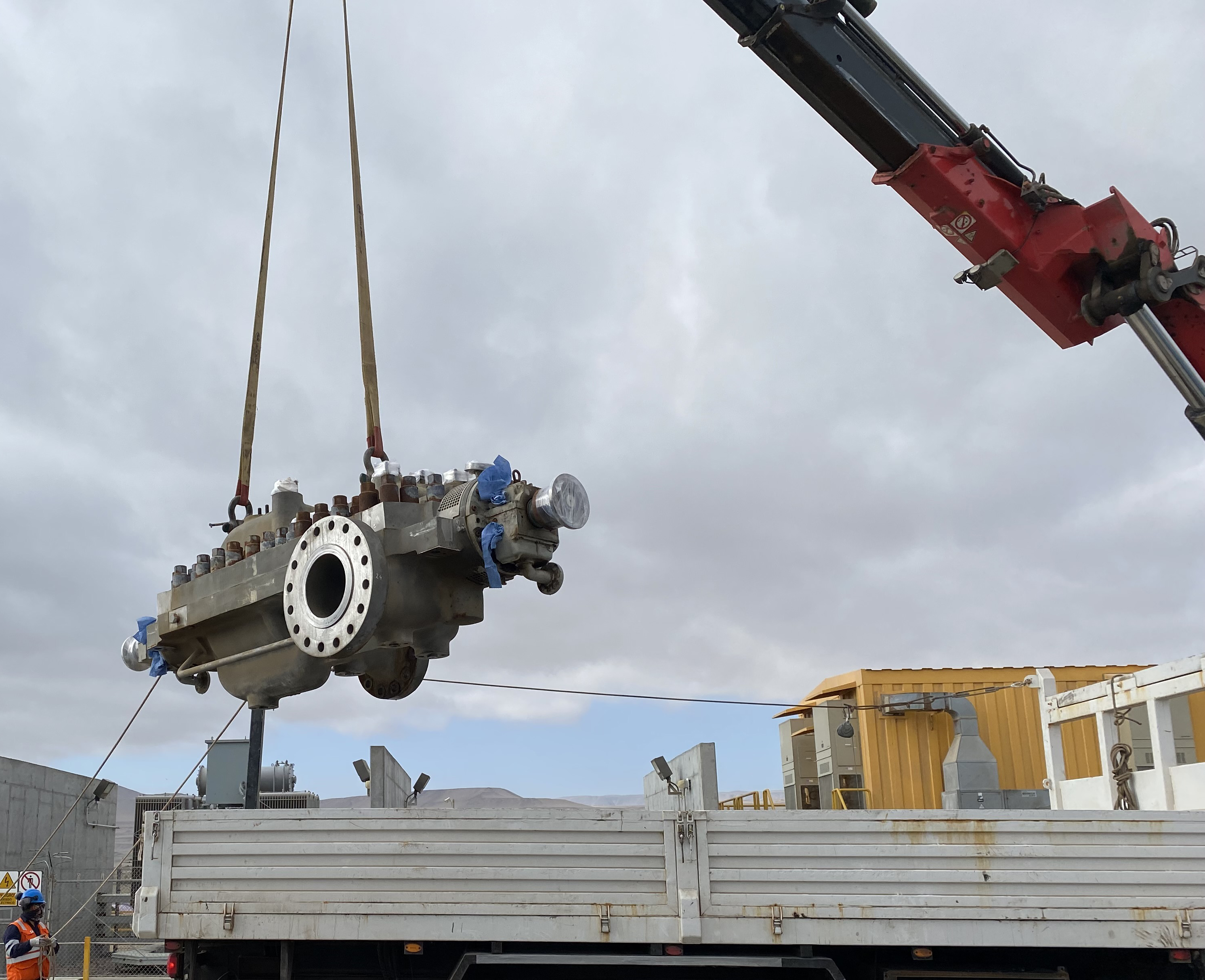
Providing through-life partnership
Trillium goes well beyond the supply of original equipment: the company provides through-life service that ensures customer support that maximizes the output value of their pumps throughout their entire life cycle, thus contributing to total plant efficiency and profitability.
Case studies showcasing the effectiveness of Floway pump service solutions in mining include a copper mine in Chile where the concentrator plant tonnage was increased. This increase led to premature damage and shortened life of the vertical turbine pump (VTP) units installed on intake structures in a process water application of the reclaimed pond system – causing operational disruptions and increased maintenance costs. Trillium substituted the VTP pumps with Floway VTSPs Vertical Turbine Solids Pumps, specifically engineered to pump fluids with solid concentrations up to 10% by weight, without changing the original motor and with little piping or foundation modification. This pump replacement resulted in an increased wear life of the pumps from an average of 300 hours to over 1000 hours and a more than three times increase in the MBTF (Mean Time Between Failures).
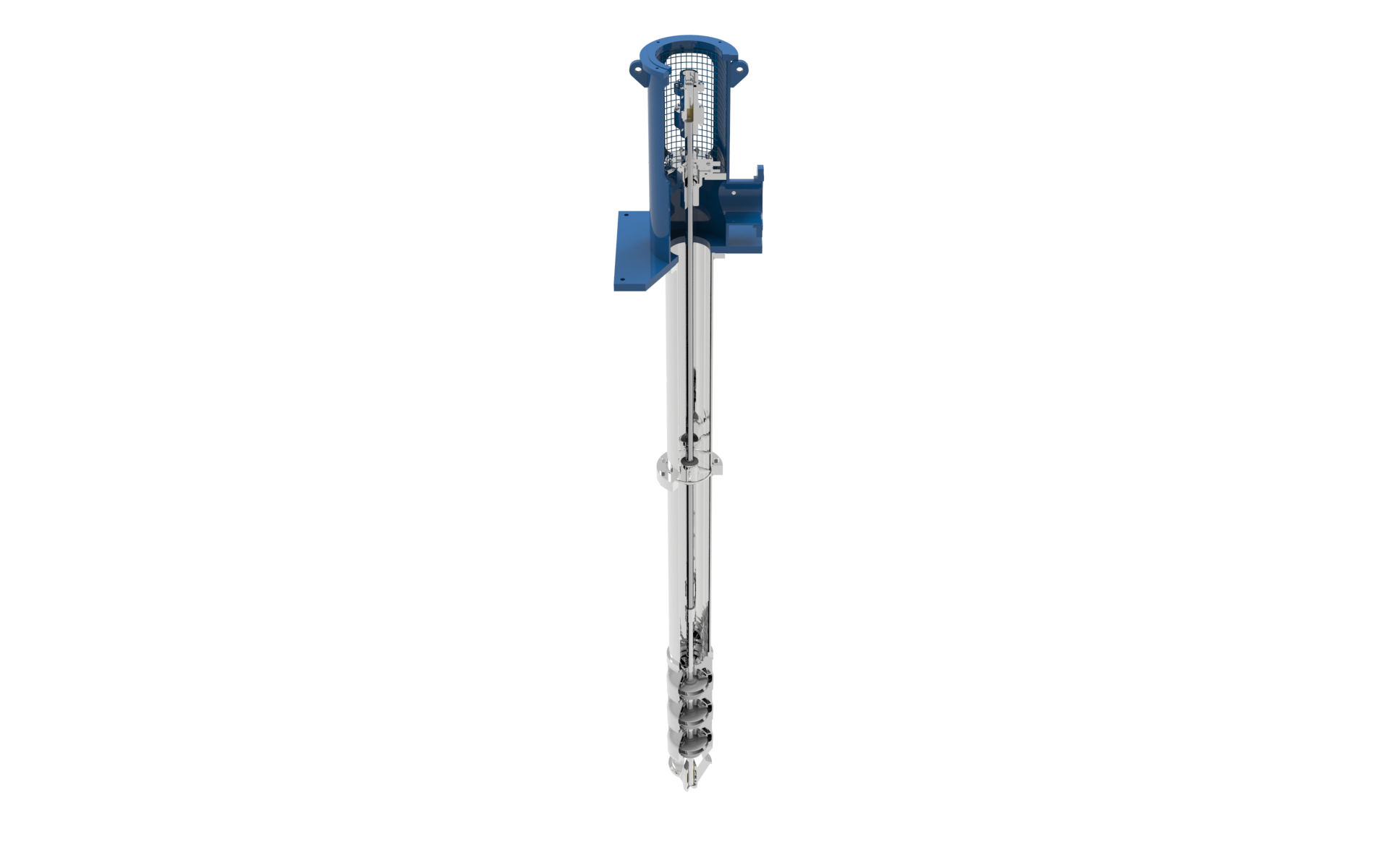
Due to its intrinsically demanding nature, the mining and mineral processing industry epitomizes the ever-increasing need for partnership-type relationships between plant operators and their equipment and service suppliers. Only through such expert collaborations will operators be able to overcome the many challenges of their projects and meet their plant efficiency, reliability and sustainability objectives.