During a shutdown, effective piping isolation is essential. If a pipe run is isolated and drained of its product, but left uncleaned and open, it poses a risk that may not be obvious.
Residual vapor from the uncleaned pipe could find its way to tees and flanges during hot work, which would be very hazardous.
So, what are the ways to prevent this from happening? and which approach is the most cost-effective?
Let’s take a look at two different methods.
Traditional Cleaning and Flushing
Repeated flushing and draining is the traditional tried-and-tested method. It works by removing any residual products and removing them in a highly-diluted form. Although effective, flushing can be incredibly labor-intensive and time-consuming. So as a result, the costs incurred can be significant.
Mechanical Isolation and Test Tools (MITT)
The alternative to flushing and draining long sections of piping is to isolate the piping locally. Using MITT tools allows you to do this by preventing any vapor from escaping. They work by using expanding rubber seals, and a water-filled annulus within the tool that hydrostatically confirms the seal.
It is important to note that these tools are used for local isolation only and not as a primary isolation point!
An important bonus is that the same tools can also be used for pressure testing – for example, after a new flange has been welded into position.
MITT-Series tools provide the opportunity to save piping isolation and testing cost in seven key areas.
7 ways Mechanical Isolation and Test Tools can reduce costs during a shutdown
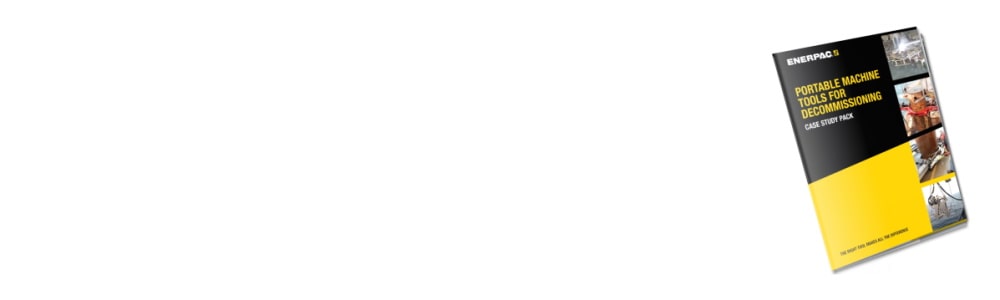
Decommissioning Case Study Pack
Learn how portable machine tools solved four tough decommissioning challenges
#1 – Reduced Downtime
Ultimately, keeping the downtime of a plant or refinery to a minimum is a key goal in any maintenance shutdown. Downtime has huge financial implications – so work needs to keep to a tight schedule. The benefits associated with the MITT methodology covered below each contribute towards achieving this.
#2 – Reduced need for Cleaning
Compared with traditional cleaning, there’s very little cleaning or steaming to be done when using MITT tools. All that is needed is a small amount of cleaning by hand. This is just in the immediate working area and can be done by the MITT operator.
#3 – Less Scaffolding
In a turnaround situation, using traditional cleaning methods often results in the need for many ‘blinding points’ – especially wherever hot work needs to be done. These points usually require scaffolding to ensure the work can be carried out safely.
Put simply, when using the MITT methodology, there’s less blinding points and fewer places where scaffolding is needed.
#4 – Reduced Water Consumption
Traditional cleaning requires many hundreds (or thousands) gallons of water to clean a full pipe run. Although paying for water consumption is a small part of cleaning costs, it’s worth mentioning that just 1 litre (1.76 pints) of water is needed when using a MITT tool.
#5 – Water Recycling
When traditional methods are used, the outcome of repeated cleaning means there’s a huge amount of water that needs to be recycled, and with this comes additional cost.
#6 – Installation and Removal of Blinds
When shutting a section of pipework, simply relying on an existing isolation valve is not sufficient because valves can (and often do) leak.
‘Blinding’ is the process where a plate is inserted to block off the supply in a section of piping. Doing this provides more reassurance that the supply is completely cut off. This method most commonly includes bolting a gasketed plate within a flanged joint.
If using MITT tools, blinding will not be needed in as many places as with more traditional methods. A separate primary isolation point will still need to be in place, but generally there should be less need for extra blinding near where hot work is to be done.
#7 – Less Manpower
Fewer technicians are needed when using the MITT method. This is because there’s less need for blinds, scaffolding, and specialist cleaning. A cost comparison exercise based on a hypothetical shutdown revealed that the number of technicians required would be halved, and the turnaround time reduced from 3 days to two. The tools are easy to use so there’s less reliance on third-party specialists. Each tool is self-centering and simple to operate, so minimal training is needed.