Marking a significant inroad to establish a South Korean foothold in the world’s gas turbine technology market, heavy industrial company Doosan Enerbility this summer began commercial operation of its first domestically produced 270-MW gas turbine and signed its first contract for a large combined cycle gas turbine power plant that will pioneer its 380-MW H-class “ultra-large” gas turbine.
The company on June 28 announced it signed a contract valued at $213 million with utility Korea Midland Power Co. (KOMIPO) for the 569-MW Boryeong New Combined Cycle Power Plant, which is slated to come online by June 2026 in Boryeong City, South Chungcheong Province. The contract also involves supply of a steam turbine and heat recovery steam generators (HRSGs). On July 28, meanwhile, Doosan began commercial operation of a 270-MW class gas turbine at the 500-MW Gimpo Combined Heat and Power (CHP) plant in Gyeonggi Province, which it developed with Korea Western Power Co. (KOWEPO).
A Significant Inroad in a Homegrown Strategy
The developments are a triumph for Doosan Enerbility, a company formerly known until March 2022 as Doosan Heavy Industries & Construction. Established in 1896, the company historically focused its power generation capabilities on building coal power plants, including much of South Korea’s giant coal-fired fleet. In the 1990s, however, Doosan kicked off development of a gas turbine, and by 2005, it proved that technical capability with the in-house development of a 5-MW gas turbine. Then, pivotally in 2013, Doosan snagged weighty participation in a national program initiated by the Ministry of Trade, Industry, and Energy (MOTIE) and the Korea Institute of Energy Technology to curb the country’s dependence on foreign imports. South Korea’s strategy sought to develop a homegrown gas turbine industry that could compete alongside the U.S., Germany, Japan, and Italy, where the world’s biggest gas turbine original equipment manufacturers (OEMs)—General Electric, Siemens Energy, Mitsubishi Power, and Ansaldo Energia—are headquartered.
![]() |
1. Korea Western Power Co. (KOWEPO) has begun commercial operation of a 270-MW gas turbine it developed with Doosan Enerbility at the 500-MW Gimpo Combined Heat and Power plant in Gyeonggi Province. South Korea’s first domestically produced gas turbine, the “K-Gas Turbine” measures a compact 11.5 meters in length and weighs 330 tons, making it smaller and lighter compared to a conventional steam turbine. Courtesy: KOWEPO |
“Gas turbine development began with the securing and development of our own technical expertise and manpower, and by establishing manufacturing facilities, process management, and test shop all in-house, we have created a system that allows an α to Ω technology implementation in one place,” Doosan noted. To accelerate progress, the company initially invested $830 million as part of the national program on research and development of a new 270-MW class large gas turbine model. By 2019, the company had cemented contracts with KOWEPO for the construction of the 500-MW Gimpo CHP plant (Figure 1). The 270-MW gas turbine (DGT6-300H.S1)—which KOWEPO has dubbed the “K-Gas Turbine”—on July 28 completed a continuous 240-hour operational test and kicked off commercial operation fired with liquefied natural gas (LNG), KOWEPO confirmed.
Milestone Achievement: First Commercial Operation
According to Doosan, the 270-MW DGT6-300H.S1 features an efficiency of more than 40%. Testing after first fire was achieved in March 2022 included state-required combustion adjustment tests, power variation tests, and emergency shutdown tests, KOWEPO noted. During the manufacturing process at Doosan’s Changwon facility in South Gyeongsang Province (where Doosan is headquartered), KOWEPO said it installed more than 3,000 instruments to assess and maintain the gas turbine’s reliability. The utility now intends to carry out 8,000 hours of demonstration operation linked to the national grid, data that will help it develop the “next generation of K-gas turbines” and support ambitions to export the model.
Driven by market forces, Doosan in tandem set out to develop the DGT6-300H.S2, a 380-MW H-class model that leverages a superalloy designed to withstand high temperatures of 1,500C and higher and features an efficiency of more than 43%. But Doosan’s recent contract with KOMIPO also includes supply of a steam turbine and HRSGs—potentially making the Boryeong New Combined Cycle Power Plant the world’s first project equipped with a South Korean–standard combined cycle gas turbine (CCGT) model.
Doosan said it has since 2021 leveraged expertise from 340 parties in South Korea’s domestic industry, academia, and research sectors to develop the CCGT model. The effort has been crucial to ensure reliability, it suggested. “The gas-fired combined cycle power plants in Korea until now had applied various types of foreign-made gas turbine models, which led to numerous difficulties in achieving efficient maintenance services,” Doosan noted.
![]() |
2. A small-scale model of Doosan Enerbility’s 380-MW hydrogen gas turbine. Courtesy: Doosan |
Working Toward a 100% Hydrogen-Fueled Gas Turbine
As part of the national project that will run until December 2027, Doosan and domestic partners are also pursuing development of a CCGT that will be ready to co-fire up to 50% hydrogen. Under that endeavor, Korea East-West Power (KEWP) will convert a 25-year-old E-class gas turbine at the Ulsan Combined Cycle Power Plant into a 270-MW H-class hydrogen gas turbine (Figure 2). The conversion could result in substantial cost savings, Doosan suggested.
“With a high-efficiency H-class hydrogen gas turbine, fuel costs can be saved by up to approximately KRW 70 billion [$53 million] annually compared to that of the existing (E-class) hydrogen gas turbines,” it says. However, that assumes average KOGAS fuel and hydrogen costs for the first half of the year, and that the 50% hydrogen gas turbine has an annual operating rate of 50%. Meanwhile, “If hydrogen is used as 50% of the fuel mix, this would lead to a maximum 21.4% reduction of carbon emissions compared to the existing 100% LNG-fueled gas turbines,” it says.
Finally, and perhaps in what could be their crowning endeavor, Doosan and South Korean partners are also separately developing a 400-MW “ultra-large” 100% hydrogen-fueled gas turbine by December 2027. “The aim is to finish development of the combustor, a key component of the 100% hydrogen-fueled gas turbine, by 2026,” Doosan said.
The tight timeline conforms to South Korea’s energy goals in its 10th Basic Plan of Long-Term Electricity Supply and Demand, which MOTIE published in January. The plan seeks to convert 28 aging coal-fired facilities to LNG power plants and build five new LNG plants, a combined 4.3 GW. That would mean “an increase in LNG power plants with an installed capacity of 43.5 GW as of 2023 to 62.9 GW by 2036,” Doosan underscored. In addition, the plan calls for the accelerated installment of hydrogen-fueled power generation capabilities. “Hydrogen-fueled power is to be increased at a rapid pace to 6.1 TWh by 2030 and 26.5 TWh by 2036,” the company said.
Hanwha Reports Record-Breaking 60% Hydrogen Co-Firing Milestone at Gas Turbine Retrofit
The urgency is also driving innovation at other technology firms in South Korea. In June, investment firm Hanwha Impact Partners reported it had successfully demonstrated hydrogen-cofiring of up to 59.5% in a Frame 7E 80-MW-class gas turbine at the Hanwha Impact Daesan plant located in Seosan, Chungnam. The power plant is sited within a petrochemical site jointly owned by Hanwha and TotalEnergies, and the test involved a decommissioned Frame 7E gas turbine-generator package that was relocated and refurbished for the “purpose-built power plant” at Daesan (Figure 3), Hanwha said.
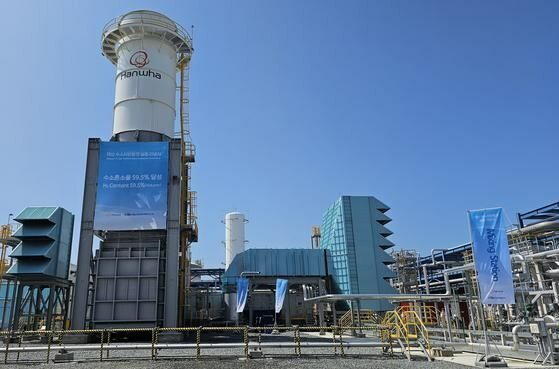
While Hanwha did not provide details about the test’s duration, it said the turbine ran “at baseload condition, dry.” The test, notably, resulted in reductions of CO2 by 22% compared to conventional LNG-fired power generation “and limited NOx emissions to 6 parts per million (ppm)—just 30% of the 20 ppm deemed acceptable by European standards—without an additional reduction device,” Hanwha said.
“This is the highest recorded co-firing rate on a medium- to large-sized gas turbine capable of commercial operation and is expected to accelerate the commercialization of hydrogen co-fired eco-friendly power generation,” the company stressed.
Combustor Within a Combustor
For the power industry, the higher hydrogen volume in a fuel blend matters, given that hydrogen and natural gas present different energy densities. As GE Power explains, “flows into a gas turbine are quoted on a volumetric basis, as this is easier to measure than heat content, but the key factor in determining emissions for a fuel blend is the relative heat input from the fuel constituents, especially as methane and hydrogen have very different energy densities. This is an important distinction as adding small amounts of hydrogen to the fuel (on a volumetric basis) will have a smaller impact on CO2 emission reduction.” That’s why achieving a 50% reduction in unit stack emissions of CO2, for example, would require a fuel blend that is about 75% hydrogen by volume. However, blending or combusting such high volumes of hydrogen has the potential to increase NOx emissions, and the actual percentage by volume of hydrogen used as a fuel and correlated CO2 emissions reductions depend on the combustion turbine or combustor model.
Hanwha’s hydrogen-to-gas turbine technology (H2GT), for which KOWEPO also played an integral role in research and development, is outfitted with FlameSheet Combustor Platform, a commercially available upgrade (for B-, E- and F-Class gas turbines) sold by three Hanwha subsidiaries: Florida-headquartered, PSM, Dutch firm Thomassen Energy, and Pangyo-headquartered Hanwha Power Systems. Originally designed to boost gas turbine flexibility, FlameSheet (Figure 4) is a “simple, two-stage radially inflow ‘combustor-within-a-combustor’ concept that allows the staged operation at each of the various loads,” the subsidiaries said.
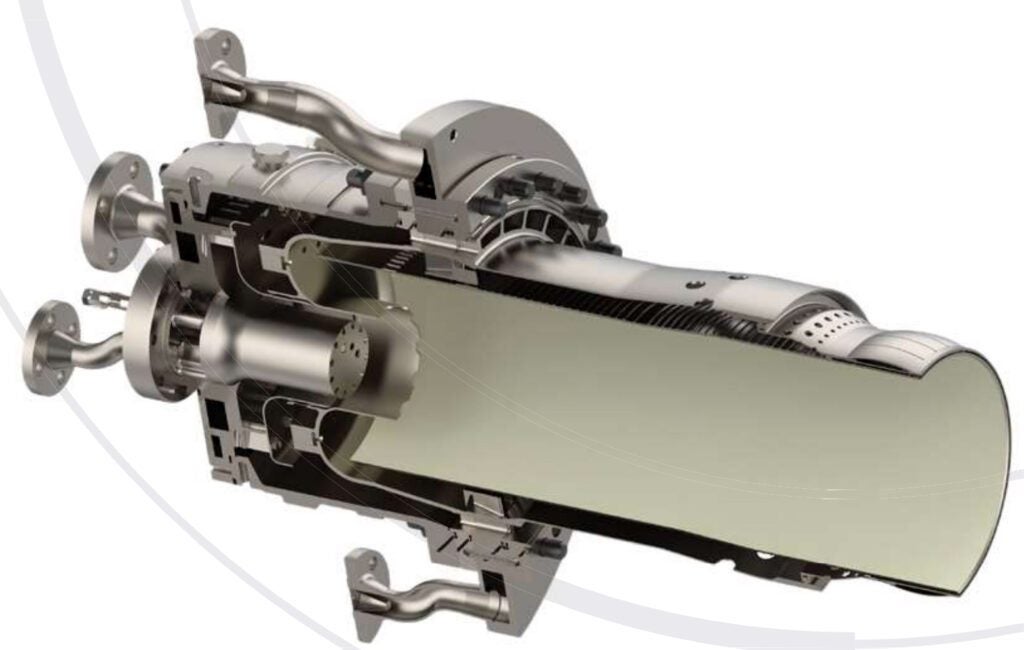
“Emissions control is more challenging when burning hydrogen as its flame temperature is significantly higher than LNG, and this, in turn, drives up NOx emissions,” Hanwha noted. Using its combustor at Daesan, Hanwha was able “to control combustion conditions without an additional reduction device to significantly reduce harmful emissions,” it said. “In addition, its flashback control technology ensured stable power generation with an increased hydrogen co-firing rate by reducing what is known as combustion flashback—a condition that sends the flame back up against the burn tube, causing damage to stable output.” Hanwha also noted that fuel delivery at the Daesan test was provided by “a proprietary designed” blending system.
Hanwha’s feat, however, is also especially remarkable for its hydrogen co-firing retrofit solution at a “stranded” LNG-fired power plant. “Doosan Heavy Industries is working to build new turbines, while we are modifying the existing old turbines to become more eco-friendly by burning hydrogen to reduce carbon dioxide,” a Hanwha Impact official told reporters when it unveiled the project in November 2022. “There are no local competitors in the field and vast opportunities exist to transform scores of antiquated gas turbines around the country.” Hanwha estimates its H2GT hybrid solution could extend the lifespan of aging LNG-fired gas turbine parts by more than 20 years.
For now, Hanwha plans to continue to develop its hydrogen co-firing technology “with the goal of attaining 100% hydrogen power generation in gas-fired turbines.” According to MOTIE, Hanwha is slated to partner with KOWEPO to develop and apply the H2GT technology to KOWEPO’s 150-MW Seoincheon Power Plant in Incheon, which is currently in commercial operation.