There are many ways to increase the efficiency of pumps. Here, Lew Beck at Oconee Nuclear Station discusses two of them: firstly the use of ceramic type coatings applied to pump internals such as the impeller and casing, and secondly through the renewal of original fits and tolerances.

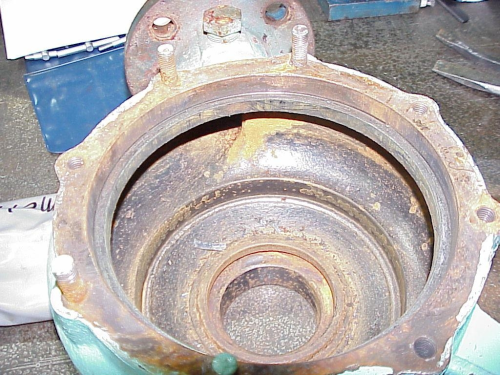

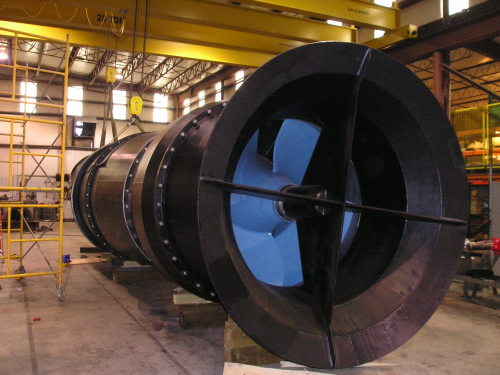
As a rotating equipment engineer in the Engineering Rapid Response Group at Oconee Nuclear Station, South Carolina, USA, my main focus is dealing with pumps. I have been involved with pump maintenance, modifications, and repairs for over 10 years. Last year, I attended the International Pump Users Symposium in Houston, Texas and was surprised to learn that pumping systems account for nearly 20% of the world’s electrical energy usage. At Duke Energy we are working to reduce the carbon footprint by improving energy efficiency. I have realized that we have an immense opportunity to impact this goal by increasing the efficiency of our pumps. The US Department of Energy (DOE) studies indicate that pumping systems account for nearly 20% of the world’s electrical energy demand and range from 25-50% of the energy usage in certain industrial plant operations. In the US, pumping systems alone account for about 25% of all industrial motors’ electricity consumption (reference Berkley Labs, Industrial Energy Analysis).Here lies the potential to capitalize on improving energy efficiency and at the same time reduce carbon output and energy costs by increasing the efficiency of our pumps at our nuclear, coal-fired, oil- and natural gas-fired, and hydroelectric power plants. So how do we increase the efficiency of our pumps? Two methods can make a significant contribution:The first method for improving the efficiency of pumps is through the use of ceramic type coatings applied to pump internals such as the impeller and casing. Oconee has used ceramic coatings such as Belzona 1341 Supermetalglide on pump internals to primarily protect against wear from abrasion and corrosion. Figures 1 and 2 show the as found condition of one of our smaller horizontal overhung pumps. Figure 3 shows the final condition of the pump casing and impeller after the epoxy coating had been applied. We have also had one of our largest pump impellers coated on a new Condenser Circulating Water (CCW) pump before being put into service. See Figures 4.
Decreasing drag
Besides the protection from the damaging effects caused by abrasion, cavitation, corrosion, and chemical attack, an added benefit to using a ceramic coating is to increase hydraulic efficiency by decreasing the effects of viscous drag and surface roughness, accentuated by the effects of erosion and corrosion. The ceramic coating is hydrophobic and creates a slick surface with low surface energy that is abrasion resistant. It produces an ultra smooth surface that reduces the boundary layer of the pumped fluid and reduces internal turbulence which improves hydraulic efficiency.The Monroe County Water Authority, in collaboration with the New York State Energy and Research Development Authority, has completed a pilot study focusing on measuring the performance and efficiency enhancement from coating the interior of pump casings with epoxy ceramic coatings. The study group of centrifugal horizontal split case pumps had been in service for a minimum of ten years. They found, in most cases, that ceramic type interior coatings increased pump efficiency by 5–10%.
Tolerance removal
The second method to increase pump efficiency on a pump that has been in service is through the renewal of its original fits and tolerances. The main culprit is usually the internal wear ring clearances. Wear rings in a centrifugal pump provide for a close running, renewable clearance, which reduces the amount of liquid leaking from the high pressure zones (discharge) to the low pressure zones (suction) in the pump. As the rings wear with use, tolerances open and more liquid passes from the discharge end back to the suction end of the pump. This increases the gross flow through the impeller, while reducing the net flow out of the pump. When the wear becomes excessive, pump performance suffers, affecting the head, capacity, and efficiency of the pump. Therefore, it becomes imperative to minimize wear ring clearances.Clearances reduced by as much as 50% increase pump performance and reliability through increased efficiency, reduced vibration, and reduced NPSHr. The efficiency gain for a typical process pump is 4–5% when clearance is reduced by 50% as referenced in the Pump User’s Handbook: Life Extension by Heinz P Bloch and Allan R Budris, page 120. Also, minimized wear ring clearances increase hydraulic damping of the rotor and reduce vibration and shaft deflection during off-design operation. It is evident that close tolerances on a pump’s wear rings have a tremendous effect on the pump’s efficiency and overall performance.Oconee Nuclear Station alone has over 800 pumps of various sizes. Some of the larger pumps such as our CCW pumps, which are Baldwin-Lima-Hamilton model SAFV 80×96 vertical single stage pumps, are high flow and low head pumps at 177,000 gpm with a design head of 28.8 ft. These 12 pumps are driven by 1750 hp Westinghouse electric motors. We currently are in the process of refurbishing these pumps which have been in service for more than 35 years. The fits and tolerances are being reestablished to the original tolerances from the pump manufacturer and in some cases a ceramic coating was applied to the impellers, as shown in Figure 4.Due to as found excess wear, particularly between the impeller and impeller housing, a conservative estimate would put efficiency gain at a minimum of 2%. As illustrated below, the cost savings of just a 2% efficiency can make a significant impact on savings. This calculation was based on the total run time of eight of the twelve CCW pumps that have been completely refurbished.Cost Per Year = (0.000189 × GPM × TDH × $ Kwh × sp.gr. × 51,600) / (Eff. Pump × Eff. Motor)Where:0.000189 = Conversion FactorGPM = Gallons per Minute = 177,000TDH = Total Dynamic Head = 28.8$ Kwh = Cost per Kilowatt-hour = .04sp.gr. = specific gravity of water = 1Eff. Pump= Pump Original Efficiency PerOEM Curve= .87Lost Eff. = .85Eff. Motor = Motor Efficiency = .93Total Hours for a twelve month period for 8 of the refurbished pumps = 51,600 hrs.Estimate with lost efficiency due to excess wear:(0.000189 × 177,000 × 28.8 × .04 × 1 × 51,600) / (.85 × .93) = $2,515,564Calculated with just a 2% increase in pump efficiency as follows:Estimate with pump efficiency reestablished:(0.000189 x 177,000 x 28.8 x .04 x 1 x 51,600) / (.87 x .93) = $2,457,734US$2,515,564 – US$2,457,734 = US$57,830(savings with just a 2% pump efficiency gain per year).
Conclusion
The ‘pump effect’ can be achieved by either applying performance enhancement coatings on the internal surfaces of pumps and/or reestablishing the manufacturer’s original fits and tolerances to the pump. This is usually accomplished by restoring wear ring clearances to the design tolerance. The coating application reduces fluid friction and the clearance change keeps internal leakage in the pump to a minimum.At Oconee Nuclear Station we have almost unknowingly been improving pump efficiency as an added benefit from performance monitoring and good maintenance practices. That is because safe and reliable operation of our pumping systems is a paramount concern for engineering and maintenance. If you consider literally the millions of pumps in service throughout the US, there is a real opportunity to reduce energy usage and the carbon footprint by just increasing the efficiency of the pumps in service by using – ‘the pump effect’.Special thanks to Oconee Maintenance: Emmett Tyree, Don Taylor, Joel Perkins and Pump Team 221 for their contributions to this article.
Oconee Nuclear Station
Capacity: 2,538 megawattsLocation: Oconee County, South CarolinaCommercial date: 1973
Oconee Nuclear Station was the first of three nuclear stations designed, built and operated by Duke Energy. Located on Lake Keowee in Oconee County, South Carolina, USA, the facility is eight miles north of Clemson. Oconee has generated more than 500 million mW/h of electricity — the first nuclear station in the US to achieve this milestone. Duke Energy’s nuclear fleet provides electricity to approximately half of its customers in the Carolinas.Oconee is the second nuclear station in the country to have its licenses renewed by the Nuclear Regulatory Commission (NRC) for an additional 20 years. All US reactors are initially licensed by the NRC for 40 years.
ContactLew BeckSenior engineer, Engineering Rapid Response Team, Reactor & electrical Systems GroupDuke EnergyOconee Nuclear StationSenecaSouth CarolinaUSATel: +1 864-885-3329E-mail: lhbeck@duke-energy.comwww.duke-energy.com