Pipe materials can be categorized into metallic and non-metallic pipes. Metallic pipes are further subdivided into ferrous and non-ferrous types. The ferrous has iron as a main component and the non-ferrous does not have iron as a main component. The carbon-steel pipes, stainless-steel pipes, chrome-moly pipes and cast-iron pipes are ferrous pipes with iron being the main component. Nickel and nickel alloy pipes, as well as copper pipes, are non-ferrous pipes. The plastic pipes, concrete pipes, special pipes such as plastic-lined pipes, glass-lined pipes and concrete-lined pipes, which may be used in special applications, are called non-metallic pipes. Ferrous pipes are the most widely-used pipes in the energy industry; carbon-steel pipes are used in abundance. The ASTM and ASME standards govern the various piping and piping materials used in the process industry.
Classification of Steel
Based on the chemical compositions, steel can be categorized into four basic groups:
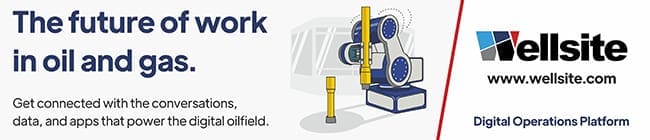
- Carbon Steel
- Alloy Steel
- Stainless Steel
- Tool Steel
Carbon steel is the most utilized steel in the industries and accounts for more than 90 percent of the total steel production. Based on the carbon content, carbon steel is further classified into three groups:
- Low Carbon Steel/Mild Steel
- Medium Carbon Steel
- High Carbon steel

In Alloy steel, varying proportions of alloying elements are used, in order to achieve desired (improved) properties such as weldability, ductility, machinability, strength, hardenability, and corrosion resistance, etc. Some of the most used alloying elements and their effects are as follows:
- Manganese – Increases strength and hardness, decreases ductility and weldability.
- Silicon – Used as deoxidizers in the steel making process.
- Phosphorus – Increases strength and hardness and decreases ductility and notch impact toughness of steel.
- Sulfur – Decreases ductility, notch impact toughness and weldability. Found in the form of sulfide inclusions.
- Copper – Improves corrosion resistance.
- Nickel – Increases hardenability and impact strength of steel.
- Molybdenum – Increases hardenability and enhances the creep resistance of low-alloy steel.
Stainless steel is an alloy steel with 10.5 percent chromium (minimum). Stainless steel exhibits extraordinary corrosion resistance due to formation of a very thin layer of Cr2O3 on the surface. This layer is also known as a passive layer. Increasing the amount of chromium will further increase the corrosion resistance of the material. In addition to chromium, nickel and molybdenum are also added to impart desired (or improved) properties. Stainless steel also contains varying amounts of carbon, silicon and manganese. Stainless steel is further classified as:
- Ferritic Stainless Steel consists of iron-chromium alloys with body-centered cubic crystal structures (BCC). These are generally magnetic and cannot be hardened by heat treatment, but can be strengthened by cold working.
- Austenitic Stainless Steel is most corrosion resistant. It is non-magnetic and non-heat-treatable. Generally, austenitic steel is highly weldable.
- Martensitic Stainless Steel is extremely strong and tough, but not as corrosion-resistant as the other two classes. This steel is highly machinable, magnetic and heat-treatable.
- Duplex Stainless Steel consists of a two-phase microstructure consisting of grains of ferritic and austenitic stainless steel (i.e., ferrite + sustenite). Duplex steel is about twice as strong as Austenitic or Ferritic Stainless Steel.
- Precipitation-Hardening (PH) Stainless Steel possesses ultra-high strength due to precipitation hardening. (Out of these five types, the first four i.e., austenitic, ferritic, martensitic and duplex, are categorized according to their crystal structure. If they are additionally strengthened by precipitation hardening process, then the product obtained is known as Precipitation-Hardening (PH) stainless steel.)
In addition to the above grades, some advanced grades (or specialty grades) of stainless steel also being used in the industries are:
- Super Austenitic Stainless steel
- Super Ferritic Stainless steel
- Super Martensitic Stainless steel
- Super Duplex Stainless steel
The austenitic stainless steel can be further divided into two types:
- Austenitic Stainless steel containing chromium and nickel as the main alloying elements (in addition to iron). These are identified as AISI 300 Series types.
- Austenitic stainless steel containing chromium, nickel and manganese as the main alloying elements (in addition to iron). These are identified as AISI 200 Series types.
Tool Steel has a high carbon content (0.5 to 1.5 percent). Higher carbon content provides greater hardness and strength. This steel is mostly used to make tools and dies. Tool steel contains various amounts of tungsten, cobalt, molybdenum and vanadium to increase the heat and wear resistance and durability of the metal. This makes tool steel ideal for use in cutting and drilling tools.
Carbon Steel Pipes
These pipes are widely used in the process industry. The designation of the pipes done by ASTM and ASME looks different, but the material grades will be the same. For example:
ASTM A 106 Gr
- A [330 Mpa]
- B [415 Mpa]
- C [485 Mpa]
The material above, when designated as per ASME standards, will be:
ASME SA 106 Gr
- A [330 Mpa]
- B [415 Mpa]
- C [485 Mpa]
The material composition and properties on both the ASME and ASTM codes will be the same other than the designation. The tensile strength of ASTM A 106 Gr A is 330 Mpa, ASTM A 106 Gr B is 415 Mpa and ASTM A 106 Gr C is 485 Mpa. The most commonly used carbon steel pipe is the ASTM A 106 Gr B. There is an alternative to the ASTM A 106 Gr A 330 Mpa, which is ASTM A 53 (hot dipped galvanized or line pipe), which is also a widely used pipe grade among carbon steel pipes. There are two types of grades in ASTM A 53 pipe:
- ASTM A 53 Gr A
- ASTM A 53 Gr B
There are three types of ASTM A 53 pipes – Type E (ERW – Electric Resistance Welded Type), Type F (Furnace and Butt Weld), Type S (Seamless). In the Type E, both ASTM A 53 Gr A and ASTM A 53 Gr B are available. In the Type F, only ASTM A 53 Gr A is available, and in the Type S again ASTM A 53 Gr A and ASTM A 53 Gr B are available. The tensile strength of ASTM A 53 Gr A pipe is similar to the ASTM A 106 Gr A, which is 330 Mpa. The tensile strength of ASTM A 53 Gr B pipe is similar to the ASTM A 106 Gr B, which is 415 Mpa. This covers the widely used carbon steel grade pipes in the process industry.
Stainless Steel Pipes
The stainless steel pipes that are mostly used in the process industry are known as austenitic stainless steel. The essential characteristic of austenitic stainless steel is that it is non-magnetic or paramagnetic. The three important specifications of austenitic stainless steel are:
- ASTM A 312 (ASME SA 312)
- ASTM A 358 (ASME SA 358)
- ASTM A 409 (ASME SA 409)
ASTM A 312 (ASME SA 312)
There are 18 grades in this specification of which the most commonly used is the 304 L. The popular category is 316 L because of its high resistance towards corrosion. The ASTM A 312 (ASME SA 312) is used for piping 8” or below in diameter. The “L” along with the grade indicates that it is low in carbon content and this enhances the weldability of the pipe grade.
ASTM A 358 (ASME SA 358)
This specification is used for pipe sizes 8” and above.
ASTM A 409 (ASME SA 409)
This specification is used for large diameter welded pipes. The pipe schedules covered in this specification are Schedule 5S and Schedule 10.
Weldability of Austenitic Stainless Steel – Austenitic stainless steel possesses higher thermal expansion than the ferritic or martensitic stainless steel. Distortion or warping occurs during the welding of austenitic stainless steel due to its high coefficient of thermal expansion and low thermal conductivity. Austenitic stainless steel is susceptible to solidification and liquation cracking. Hence, proper care to be given while selecting filler material and welding process. Submerged arc welding (SAW) is not preferred when fully austenitic stainless steel or low ferrite content weld deposit is required. Table (Appendix – 1) is a guide for the selection of proper filler wire or welding rods, as per the base material (for austenitic stainless steel).
Chrome-Moly Pipes
The chrome-moly pipes are suitable for high temperature service lines because the tensile strength of the chrome- moly pipes is maintained during the high temperature. This pipe finds its application in power plants, heat exchangers, etc. The specification of this pipe is ASTM A 335 with multiple grades:
- P1 & P2 – 380 Mpa
- P12 – 415 Mpa
- P23 – 510 Mpa
- P24 – 585 Mpa
- P91 – 585 Mpa (Type 1 and Type 2)
- P92 & P911 – 620 Mpa
- P122 – 620 Mpa
- P36 – 660 Mpa
- Other grades – 415 Mpa
Cast Iron Pipes
Cast iron pipes are used in services such as fire protection, drains, sewage, heavy load (subjected to heavy load) – underground pipes, etc. The grades of cast iron pipes are:
- Ductile Iron Pipe
- Dur Iron Pipe
The ductile iron pipe is used in underground piping for fire protection service. The dur iron pipe is hard due to the fact that it contains silicon. These pipes are used in commercial acid services, as this grade shows resistance to commercial acids, as well as used in water treatment where acidic wastes are discharged.

References
- ASTM A312 / A312M – 19 – Standard Specification for Seamless, Welded, and Heavily Cold Worked Austenitic Stainless Steel Pipes
- ASTM A358 / A358M – 19 Standard Specification for Electric- Fusion-Welded Austenitic Chromium-Nickel Stainless Steel Pipe for High-Temperature Service and General Applications
- ASTM A409 / A409M – 19 Standard Specification for Welded Large Diameter Austenitic Steel Pipe for Corrosive or High- Temperature Service
- Process Piping B31.3 – 2020
- Power Piping B31.1 – 2020
- 2019 ASME Boiler and Pressure Vessel Code, Section VIII, Division 1
- 2019 ASME Boiler and Pressure Vessel Code, Section VIII, Division 2
- 2019 ASME Boiler and Pressure Vessel Code, Section VIII, Division 3